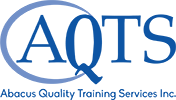
10%
(Copy /paste this coupon code in the cart at the time of checkout)
Course Overview
Kaizen is perhaps one of the most commonly used terms when it comes to process improvement methodologies. Kaizen is a Japanese term meaning “Change for the better” or “improvement”. It originates from two Japanese words – “kai” which means “change” or “to correct” and “zen” which means “good”. It is most commonly translated into English as “Continuous Improvement”. It works on the basis that nothing can ever become perfect, and there is always something that can be improved. It is used to bring about small, incremental improvements, which, if pursued for some time and in proper manner, compound to very significant results. It involves all the employees of the organization – from the top management as well as the bottom level.
Kaizen training is designed to help participants understand the basic principles of operational excellence, Kaizen tools, and techniques, as well as their practical application in the workplace. Kaizen tools seek to solve problems through scientific methods, based on teamwork. It is a daily improvement of all employees and all company operations.
Participants learn everything about Kaizen implementation. In Kaizen Training you will learn the methods and steps to successfully implement lean and change processes across the enterprise.
On completion, successful students will have the knowledge to:
This course is designed to impart professional level knowledge of the concepts related to quality system. The course contents will cover;
AQTS reserves the right to cancel or re-schedule the course and to change the course instructors. In the event of course cancellation, AQTS will not be responsible for airfare penalties or other travel related expenses that you may incur.
If you cannot find a substitute, we can transfer your course fees to the same course in next offering.
A Certificate will be issued to attendees who participate in the entire course.
There are no prior knowledge requirements for this course; however, it may be beneficial for participants to have knowledge of Kaizen.