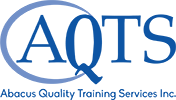
10%
(Copy /paste this coupon code in the cart at the time of checkout)
Course Overview
A circle is team consisting of 4 to 8 people who meet regularly to identify and solve problems. The concept of Quality Circles originated in Japan after World War II. It was an outgrowth of massive training programs undertaken by the Japanese in early 1950’s. This training started at the top of the companies and progressed down through the hierarchies, level by level, until it included the first line of supervision. Each trained manager had concluded “I can do a better job on quality if my subordinates are similarly trained in how to attain and improve quality.” The success of Quality Circles in Japan led many managers in the US to believe that they too can make them successful. Quality Circles were rechristened in US by various names like Small Group Activity etc. The groups/circles apart from having quality as a major consideration tried to improve internal efficiencies of the company by improving methods, productivity and /or reducing manufacturing costs. The circles need to be trained in basics of Quality Circles functioning and problem solving tools such as Check Sheets, Cause and Effect Diagrams, Pareto, Histogram, Stratification, Scatter Diagrams, Control Charts, Brainstorming, Flow Charts and 5 Why Analysis. They undertake out one or more improvement projects to learn how to apply the techniques and training. Quality Circles make periodic management presentations about their respective projects on a continuous basis.
The one day training course will allow the participants to understand the Quality Circle Concept. It shall allow them to learn History, Characteristics, Benefits, Requirements, Formation and Reasons for failure of Quality Circles. Participants will also learn how to apply problem solving tools at various steps of problem solving process in quality circles.
AQTS reserves the right to cancel or re-schedule the course and to change the course instructors. In the event of course cancellation, AQTS will not be responsible for airfare penalties or other travel related expenses that you may incur.
If you cannot find a substitute, we can transfer your course fees to the same course in next offering.
A Certificate will be issued to attendees who participate in the entire course.
This one day training course will be useful for supervisors, engineers and managers from areas such as Human Resources, Marketing, Sales, Design, Planning, Manufacturing, Materials, Maintenance, Logistics, Service and Quality Assurance from both manufacturing and service organizations.